فهرست عناوین
- بررسی علمی مراحل شیمیایی فرآیند استوالد در تولید اسید نیتریک
- * مرحله اول: اکسایش کاتالیستی آمونیاک به مونوکسید نیتروژن
- *مرحله دوم: اکسایش مونوکسید نیتروژن به دی اکسید نیتروژن
- *مرحله سوم: جذب دیاکسید نیتروژن برای تشکیل اسید نیتریک
- نقش آمونیاک در تولید اسید نیتریک و واکنش های حیاتی آن
- اهمیت کاتالیزور پلاتینیوم در مرحله اول فرآیند استوالد
- مکانیزم تشکیل مونوکسید نیتروژن (NO) و کنترل شرایط دما و فشار
- *کنترل دما و فشار
- *واکنش های جانبی و پیشگیری از آن ها
- چگونگی تبدیل NO به N2O3، N2O4 و در نهایت اسید نیتریک
- تنظیم واکنش های میانی در فرآیند استوالد : از NO2 تا اسید نیتریک
- کاتالیزورها و مواد افزودنی جایگزین در بهبود راندمان فرآیند استوالد
- مدل سازی ترمودینامیکی و سینتیکی در مراحل تولید اسید نیتریک
- ابزارهای صنعتی و طراحی راکتور در فرآیند استوالد : دستیابی به بالاترین بهره وری
- ایمنی و ریسک های عملیاتی در واحدهای تولید اسید نیتریک به روش استوالد
- *خطرات مرتبط با مواد اولیه و محصولات
- *خطرات عملیاتی
- *روشهای پیشگیرانه
- نقش بازیافت انرژی و مبدل های حرارتی در مراحل تولید اسید نیتریک
- آینده فرآیند استوالد: نوآوری در کاتالیزور ، فناوری سبز و کاهش آلایندگی
نوشته شده توسط شرکت صنایع نیتریک ایران
منتشر شده توسط شرکت صنایع نیتریک ایران
تاریخ انتشار مقاله : 07-10-1403
تاریخ بروزرسانی مقاله : 07-10-1403
تعداد کلمات : 2900
آدرس مقاله : لینک مقاله
مراحل شیمیایی فرآیند استوالد در تولید اسید نیتریک
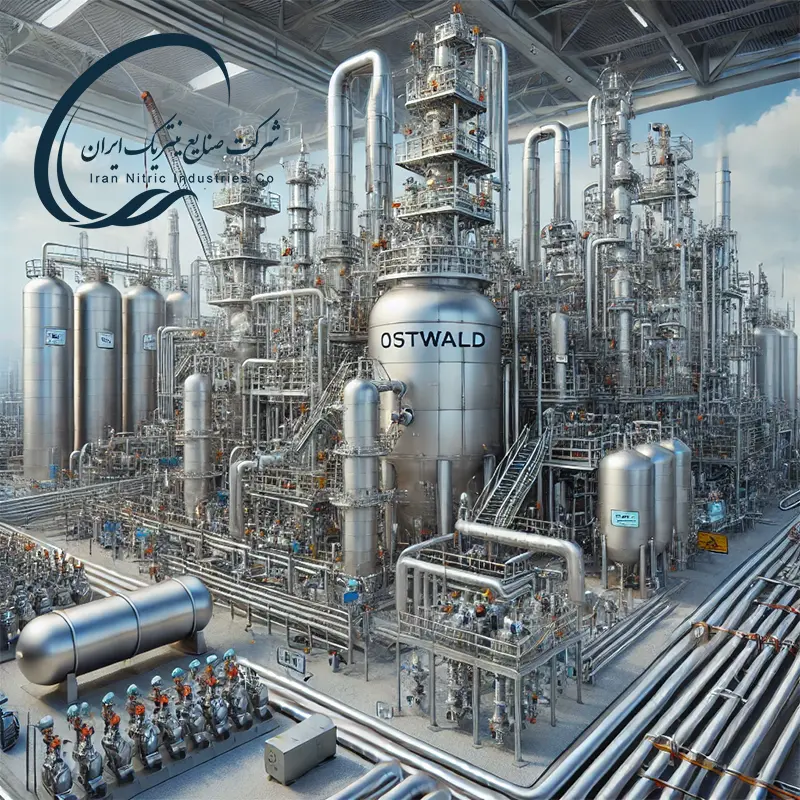
بررسی علمی مراحل شیمیایی فرآیند استوالد در تولید اسید نیتریک
فرآیند استوالد ، روش صنعتی اصلی تولید اسید نیتریک ، شامل سه مرحله کلیدی است. که هر کدام از نظر ترمودینامیک و سینتیک شیمیایی ، دارای پیچیدگی هایی هستند.
* مرحله اول: اکسایش کاتالیستی آمونیاک به مونوکسید نیتروژن
واکنش: 4NH₃(g) + 5O₂(g) ⇌ 4NO(g) + 6H₂O(g)
این واکنش گرمازا (ΔH = -905 kJ/mol) است. و در حضور کاتالیست پلاتین-رودیوم (Pt-Rh) روی شبکه ای از سیم های گازی یا شبکه های فلزی سرامیکی انجام می شود. دمای عملیاتی بالا (850-900 درجه سانتیگراد) برای غلبه بر انرژی فعال سازی بالا و سرعت بخشی به واکنش ضروری است.
فشار معمولاً بین 4 تا 10 اتمسفر است. و نسبت آمونیاک به هوا دقیقاً کنترل می شود. تا از اکسیداسیون کامل آمونیاک به نیتروژن (N₂) جلوگیری شود زیرا که واکنشی نامطلوب است. مکانیسم دقیق این واکنش پیچیده است و هنوز هم موضوع تحقیقات فعال است. با این حال ، به طور کلی پذیرفته شده است .که آمونیاک ابتدا روی سطح کاتالیست جذب می شود.
و سپس به طور تدریجی اکسید می شود. نقش کاتالیست پلاتین-رودیوم ، کاهش انرژی فعال سازی واکنش و افزایش سرعت آن است. محصولات جانبی مانند N₂O نیز به میزان کم تولید می شوند. دمای بالا برای رسیدن به تعادل مطلوب مورد نیاز است. با این حال ، دمای بسیار بالا می تواند منجر به افزایش تولید N₂ می شود. کاتالیست نقش حیاتی در افزایش سرعت واکنش تولید اسید نیتریک و دستیابی به راندمان بالا دارد.
*مرحله دوم: اکسایش مونوکسید نیتروژن به دی اکسید نیتروژن
واکنش: 2NO(g) + O₂(g) ⇌ 2NO₂(g)
این واکنش نسبتاً کند و گرمازا نیست (ΔH = -114 kJ/mol) . برای افزایش سرعت واکنش ، دما معمولاً در حدود 50 درجه سانتیگراد حفظ می شود. و فشار نزدیک به فشار اتمسفر است. زمان اقامت کافی برای تکمیل واکنش ضروری است. این واکنش یک واکنش دو مولکولی است که شامل برخورد مستقیم دو مولکول NO و یک مولکول O₂ است. هیچ کاتالیستی در این مرحله مورد نیاز نیست.
دمای پایین تر در این مرحله به نفع تعادل و تشکیل NO₂ است. با این حال ، دما نباید آنقدر پایین باشد. که سرعت واکنش به شدت کاهش یابد. زمان اقامت گازها در راکتور برای تکمیل واکنش و رسیدن به تبدیل مناسب NO به NO₂ مهم است.
*مرحله سوم: جذب دیاکسید نیتروژن برای تشکیل اسید نیتریک
واکنش.: 3NO₂(g) + H₂O(l) → 2HNO₃(aq) + NO(g)
این واکنش در برج های جذب انجام می شود. که در آن دی اکسید نیتروژن با آب در تماس است. دمای برج جذب نسبتا پایین (حدود 20-30 درجه سانتیگراد) نگه داشته می شود. NOتولید شده در این مرحله ، معمولا به مرحله دوم بازگردانده می شود تا دوباره به NO₂ اکسید شود.
دی اکسید نیتروژن در آب حل میشود و با آب واکنش میدهد تا اسید نیتریک و مونوکسید نیتروژن تولید کند. حفظ دمای پایین و افزایش سطح تماس دیاکسید نیتروژن با آب ، در افزایش راندمان جذب ضروری است. طراحی برج های جذب به گونه ای است که حداکثر تماس بین گاز و مایع فراهم شود.
نقش آمونیاک در تولید اسید نیتریک و واکنش های حیاتی آن
آمونیاک (NH₃) ماده اولیه حیاتی در تولید اسید نیتریک از طریق فرآیند استوالد است. خلوص بالای آمونیاک برای به دست آوردن راندمان بالا و جلوگیری از آلودگی اسید نیتریک تولید شده ضروری است. در این فرآیند ، آمونیاک در حضور کاتالیست پلاتین-رودیوم در دمای بالا و فشار متوسط ، با اکسیژن هوا واکنش داده و به مونوکسید نیتروژن (NO) تبدیل میشود (4NH₃ + 5O₂ → 4NO + 6H₂O).
این واکنش گرمازا بوده و میزان مصرف آمونیاک در روند تولید ، به میزان تقاضا برای خرید سید نیتریک شیراز بشکه 220 لیتری وابسته است. که در تولید کودهای نیتروژنه و سایر مواد شیمیایی نقش حیاتی دارد. تبدیل شیمیایی آمونیاک به NO اولین و مهمترین مرحله در فرآیند استوالد است. چرا که راندمان این مرحله به طور مستقیم بر بازده کل فرآیند تأثیر میگذارد.
اهمیت کاتالیزور پلاتینیوم در مرحله اول فرآیند استوالد
کاتالیزور پلاتین (اغلب آلیاژ Pt-Rh) در مرحله اول فرآیند استوالد ، اکسایش آمونیاک به NO را با سرعت و بازده بالا میسر می سازد. ویژگی های پلاتین مانند فعالیت کاتالیستی بالا ، پایداری حرارتی و توانایی جذب آمونیاک و اکسیژن ، آن را به گزینه مناسبی تبدیل میکند.
دمای بالا (850-950 درجه سانتیگراد) و فشار متوسط (4-10 اتمسفر) برای واکنش ضروری اند. ساختار فیزیکی کاتالیزور (سطح ویژه و تخلخل) نیز بر راندمان تأثیرگذار است. با این حال ، دمای بالا و گونه های خورنده واکنش ، موجب فرسایش تدریجی پلاتین می شود ، که یک چالش مهم در فرآیند است.
مکانیزم تشکیل مونوکسید نیتروژن (NO) و کنترل شرایط دما و فشار
مکانیسم دقیق تشکیل مونوکسید نیتروژن (NO) در مرحله اول فرآیند استوالد روی سطح کاتالیزور پلاتین بهطورکلی شامل مراحل زیر است.:
-مولکولهای آمونیاک (NH₃) و اکسیژن (O₂) روی سطح کاتالیزور پلاتین جذب می شوند. پلاتین به دلیل ساختار الکترونی خاص خود ، توانایی جذب و فعالسازی این مولکول ها را دارد.
-پیوندهای شیمیایی در مولکولهای جذب شده ضعیف شده و شکسته می شوند. این مرحله انرژی فعالسازی بالایی دارد. و به همین دلیل به دمای بالا نیاز است. در این مرحله ، گونه های واسطه فعال مانند اتم های نیتروژن (N) و اکسیژن (O) تشکیل می شوند.
-گونه های واسطه فعال روی سطح کاتالیزور با یکدیگر واکنش می دهند. و مونوکسید نیتروژن (NO) را تشکیل می دهند. این واکنشها بسیار پیچیده هستند و شامل تشکیل و تجزیه چندین گونه واسطه است.
-مولکول های NO تشکیلشده از سطح کاتالیزور دِسربشن (رها) می شوند.
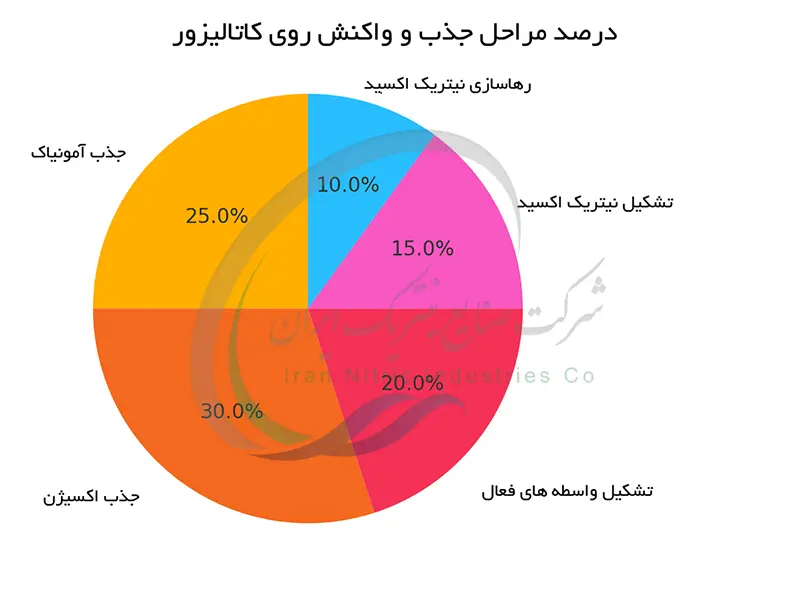
*کنترل دما و فشار
دمای بالا (850-950 درجه سانتیگراد) انرژی فعال سازی موردنیاز برای شکستن پیوندهای N-H و O=O را فراهم می کند. و تشکیل NO را تسریع می بخشد. فشار متوسط (4-10 اتمسفر) غلظت واکنش دهنده ها را افزایش می دهد. و میزان واکنش را بهبود می بخشد.
*واکنش های جانبی و پیشگیری از آن ها
تشکیل نیتروژن (N₂) یک واکنش جانبی نامطلوب است. که بازده NO را کاهش می دهد. برای حداقل کردن این واکنش جانبی ، باید.:
-دما به دقت کنترل شود
-نسبت O₂/NH₃ به دقت کنترل شود
-طراحی مناسب برای راکتور صورت گیرد
-استفاده از کاتالیزور با فعالیت و انتخاب پذیری بالا
چگونگی تبدیل NO به N2O3، N2O4 و در نهایت اسید نیتریک
در روش استوالد تولید نیتریک ، تبدیل NO به اسید نیتریک شامل چند مرحله و واکنش های شیمیایی است که در زیر توضیح داده میشود.:
1. اکسیداسیون NO به NO₂ : مونوکسید نیتروژن (NO) که در مرحله اول فرآیند تولید می شود. با اکسیژن اضافی واکنش داده و به دی اکسید نیتروژن (NO₂) تبدیل می شود. این واکنش گرمازا و نسبتاً کند است ، بنابراین برای تسریع آن ، از یک رآکتور با دمای کنترل شده (حدود 50 درجه سانتیگراد) و فشار کمی بالاتر از فشار اتمسفر استفاده می شود.
2NO(g) + O₂(g) ⇌ 2NO₂(g) ΔH < 0
2. تشکیل دینیتروژن تتراکسید (N₂O₄) : دی اکسید نیتروژن (NO₂) در دمای پایینتر ، بهطور خود به خودی به دی نیتروژن تتراکسید (N₂O₄) دی مر می شود. این واکنش گرمازا و نیز برگشتپذیر است.
2NO₂(g) ⇌ N₂O₄(g) ΔH < 0
کاهش دما ، تعادل را به سمت تشکیل N₂O₄ جابجا می کند. در عمل ، مخلوطی از NO₂ و N₂O₄ وجود دارد. که به برج جذب منتقل می شود . N₂O₃ به طور مستقیم در این مراحل تشکیل نمی شود.
3. جذب در برج و تولید اسید نیتریک : مخلوط NO₂ و N₂O₄ به برج جذب منتقل می شود. که در آن با آب واکنش داده و اسید نیتریک (HNO₃) و مونوکسید نیتروژن (NO) تولید می شود. این واکنش یک واکنش اکسیداسیون-کاهشی است. که در آن NO₂ به عنوان اکسید کننده و آب به عنوان کاهنده عمل میکند.
3NO₂(g) + H₂O(l) → 2HNO₃(aq) + NO(g)
در فرآیند استوالد ، NO ابتدا با اکسیژن به NO₂ اکسید می شود. که در دماهای پایین تر به N₂O₄ تبدیل می شود. سپس ، مخلوط NO₂/N₂O₄ در یک برج جذب با آب واکنش داده و اسید نیتریک (HNO₃) تولید می کند. NO تولید شده در این مرحله مجدداً به فرآیند بازگردانده می شود تا بازده افزایش یابد. کنترل دما ، فشار ، و طراحی برج جذب (به ویژه جریان متقابل) برای بهینه سازی فرآیند ضروری است.
تنظیم واکنش های میانی در فرآیند استوالد : از NO2 تا اسید نیتریک
تنظیم واکنش های میانی در فرآیند استوالد از NO₂ به اسید نیتریک برای حداکثر کردن راندمان تولید و جلوگیری از تشکیل محصولات جانبی نامطلوب حیاتی است. این تنظیم شامل موارد زیر است:
-زمان تماس (Residence Time): زمان تماس بین NO₂ و N₂O₄ و آب در برج جذب باید به دقت کنترل شود. زمان تماس کم باعث تبدیل ناکافی NO₂ به اسید نیتریک و زمان تماس زیاد ممکن است. منجر به تشکیل محصولات جانبی ناخواسته یا کاهش سرعت واکنش شود. بهینه سازی این زمان به عوامل مختلفی از جمله طراحی برج ، سرعت جریان گاز و مایع و غلظت NO₂ بستگی دارد.
-کنترل دما : واکنش بین NO₂ و آب گرمازا است. دمای بالای برج جذب منجر به تجزیه اسید نیتریک یا تشکیل محصولات جانبی می شود. بنابراین ، کنترل دمای برج با استفاده از سیستم های خنککننده مانند مبدلهای حرارتی ، ضروری است. دمای بهینه معمولا بین 30 تا 40 درجه سانتیگراد است.
-مدیریت غلظت ورودی : غلظتهای ورودی NO₂ و آب باید به دقت تنظیم شوند. غلظت بالای NO₂ منجر به افزایش دمای واکنش و در نتیجه کاهش راندمان می شود. در حالی که غلظت پایین NO₂ می تواند منجر به واکنش آهسته و تولید ناکافی اسید نیتریک گردد. نسبت NO₂ به آب نیز اهمیت زیادی دارد تا راندمان تولید را به حداکثر برساند. و از تشکیل محصولات جانبی جلوگیری شود.
تنظیم صحیح زمان تماس ، دما و غلظت ها برای دستیابی به حداکثر راندمان تولید اسید نیتریک و کیفیت محصول مطلوب ، در فرآیند استوالد امری ضروری است. این تنظیم ها اغلب با استفاده از مدل سازی ریاضی و داده های تجربی به دست آمده و به طور پیوسته در واحدهای صنعتی پایش و تنظیم می شود.
کاتالیزورها و مواد افزودنی جایگزین در بهبود راندمان فرآیند استوالد
تحقیقات اخیر بر روی کاتالیزورهای جایگزین برای پلاتین در فرآیند استوالد تمرکز دارند. تا راندمان را افزایش داده و مصرف انرژی را کاهش دهند. پالادیوم و آلیاژهای چندفلزی به عنوان گزینه های امیدوارکننده ظاهر شده اند. که فعالیت کاتالیزوری بالاتری نسبت به پلاتین در برخی شرایط نشان می دهند. علاوه بر این ، استفاده از مواد کمکی (Promoter) مانند اکسیدهای فلزی یا مواد نانو ساختار برای افزایش پایداری کاتالیزور و انتخابپذیری به سمت محصول مورد نظر (NO) در حال بررسی است.
این پژوهش ها شامل طراحی کاتالیزورهای با ساختارهای جدید و بررسی تأثیر عوامل مختلف مانند اندازه ذرات ، مورفولوژی و ترکیب شیمیایی بر روی فعالیت و پایداری آن ها می باشند. هدف نهایی یافتن کاتالیزوری با هزینه کمتر ، پایداری بالاتر ، و راندمان بیشتر در تولید NO در مرحله اول فرآیند استوالد است.
موضوع | توضیحات |
---|---|
ماده اولیه | آمونیاک (NH₃) |
خلوص آمونیاک | خلوص بالا برای بهبود راندمان و کاهش آلودگی اسید نیتریک تولیدی |
واکنش اصلی | \(4NH₃ + 5O₂ → 4NO + 6H₂O\) |
کاتالیست | پلاتین-رودیوم |
شرایط واکنش | دمای بالا (حدود 900 درجه سانتیگراد) و فشار متوسط (حدود 4-10 اتمسفر) |
محصول اولیه | مونوکسید نیتروژن (NO) |
واکنش گرمازا | بله، واکنش گرمازا با تولید انرژی قابل توجه |
واکنش ثانویه | NO در حضور اکسیژن به دیاکسید نیتروژن (NO₂) اکسید میشود \(2NO + O₂ → 2NO₂\) |
جذب نهایی | NO₂ در آب حل شده و اسید نیتریک (HNO₃) تولید میشود \(3NO₂ + H₂O → 2HNO₃ + NO\) |
وابستگی مصرف آمونیاک | وابسته به تولید کودهای نیتروژنه، مواد منفجره، و صنایع شیمیایی |
اهمیت مرحله اولیه | تأثیر مستقیم راندمان این مرحله بر بازده کل فرآیند |
کاربردهای نهایی اسید نیتریک | تولید کودهای نیتروژنه |
مدل سازی ترمودینامیکی و سینتیکی در مراحل تولید اسید نیتریک
مدل سازی ترمودینامیکی و سینتیکی در فرآیند استوالد ، به طراحان واحدهای صنعتی کمک می کند. تا شرایط بهینه عملیاتی را تعیین کنند. مدل های ترمودینامیکی ، با استفاده از پارامترهایی مانند آنتالپی ، آنتروپی و انرژی آزاد گیبس ، تعادل واکنش ها در هر مرحله را پیشبینی می کنند. و تاثیر دما و فشار بر روی میزان تبدیل مواد اولیه به محصولات را نشان می دهند.
مدلهای سینتیکی ، سرعت واکنش ها را بر اساس مکانیسم های واکنش و ثابت های سرعت پیش بینی می کنند. این مدل ها میتوانند. با استفاده از نرمافزارهای شبیهسازی مانند CFD (دینامیک سیالات محاسباتی) و با در نظر گرفتن مدل های رآکتور ایدهآل مانند رآکتورهای پیوسته هم زده شده (CSTR) یا رآکتورهای لوله ای (PFR) توسعه یابند.
در مدلسازی ، به دست آوردن اطلاعات دقیق در مورد ثابت های سرعت و همچنین پارامترهای ترمودینامیکی (مانند ΔH, ΔS, ΔG ) اهمیت زیادی دارد. این اطلاعات از طریق آزمایش ها و داده های تجربی به دست میآیند. با استفاده از این مدل ها ، می توان تاثیر پارامترهای عملیاتی (مانند دما، فشار، غلظتها و زمان ماند) بر روی راندمان تولید ، انتخاب پذیری و تشکیل محصولات جانبی را ارزیابی کرد. و در نتیجه شرایط بهینه برای به حداکثر رساندن راندمان تولید اسید نیتریک و کاهش مصرف انرژی تعیین شود.
ابزارهای صنعتی و طراحی راکتور در فرآیند استوالد : دستیابی به بالاترین بهره وری
در فرآیند استوالد ، دستیابی به بالاترین بهره وری مستلزم طراحی دقیق راکتور و انتخاب ابزارهای صنعتی مناسب است. انتخاب نوع راکتور (مانند راکتورهای لوله ای یا راکتورهای بستر ثابت) ، جنس بدنه مقاوم در برابر خوردگی ناشی از اسید نیتریک ، و طراحی بهینه بستر کاتالیزوری (شامل اندازه، شکل و توزیع ذرات کاتالیست) برای به حداکثر رساندن تماس بین واکنشدهندهها و کاتالیست حیاتی است.
مدیریت جریان های رفت و برگشتی ، به ویژه بازیافت گازهای NOx و کنترل دقیق دما و فشار در راکتور ، برای افزایش راندمان تولید اسید نیتریک ضروری است. همچنین ، بازیافت حرارت از جریان های خروجی واکنش برای پیش گرم کردن جریان های ورودی به راکتور ، نقش مهمی در کاهش مصرف انرژی و افزایش بهره وری کلی فرآیند ایفا میکند.
ایمنی و ریسک های عملیاتی در واحدهای تولید اسید نیتریک به روش استوالد
در اینجا برخی از خطرات و روشهای پیشگیرانه مرتبط با فرآیند استوالد آمده است:
*خطرات مرتبط با مواد اولیه و محصولات
-آمونیاک یک گاز سمی و قابل اشتعال است. نشت آمونیاک باعث سوختگی شیمیایی پوست ، چشم و سیستم تنفسی می شود. و در غلظتهای بالا منجر به خفگی شود. همچنین ، مخلوط آمونیاک و هوا می تواند منفجر شود.
-اکسیدهای نیتروژن مانند NO و NO₂ گازهای سمی و خورنده هستند. که باعث آسیب جدی به سیستم تنفسی ، چشم ها و پوست می شوند.
-اسید نیتریک یک مایع بسیار خورنده است که باعث سوختگی شیمیایی شدید پوست ، چشم و سایر بافتها می شود. تماس با اسید نیتریک می تواند به فلزات نیز آسیب برساند.
- اگرچه خود پلاتین سمی نیست ، اما ذرات پلاتین می توانند. در فرآیند استوالد آزاد شوند و در نتیجه مشکلاتی برای محیط زیست و سلامتی ایجاد کنند.
*خطرات عملیاتی
-در برخی مراحل فرآیند استوالد ، فشار بالا وجود دارد که باعث نشت یا انفجار می شود.
-دمای بالا در رآکتور و سایر بخش های فرآیند ، ریسک آتش سوزی و سوختگی را افزایش میدهد.
-اسید نیتریک و سایر مواد شیمیایی مورد استفاده در این فرآیند ، بسیار خورنده هستند و می توانند به تجهیزات و لوله ها آسیب برسانند و منجر به نشت شوند.
-برخی از واکنش ها در فرآیند استوالد گرمازا هستند. و باعث افزایش ناگهانی دما و فشار می شود.
- در واحدهای صنعتی ، امکان بروز خطرات الکتریکی وجود دارد.
*روشهای پیشگیرانه
-استفاده از سیستم های تشخیص نشت گاز
-سیستم های تهویه و اگزاست
-سیستم های اطفاء حریق
-لباس های محافظ شخصی (PPE)
-آموزش پرسنل
-مراقبت و نگهداری تجهیزات
-مدیریت ریسک
-سیستم های قفل و کلید
-طراحی فرایند ایمن
نقش بازیافت انرژی و مبدل های حرارتی در مراحل تولید اسید نیتریک
بهینه سازی مصرف انرژی در این فرآیند از طریق طراحی سیستم های بازیافت حرارت و استفاده از مبدل های حرارتی با بازده بالا ، از اهمیت بالایی برخوردار است. گرمای آزاد شده در این واکنش ها میتواند به منظور پیش گرم کردن جریان های ورودی به مراحل بعدی فرآیند (مانند پیش گرم کردن هوا یا آمونیاک) مورد استفاده قرار گیرد. این کار با استفاده از مبدل های حرارتی مناسب ، که می توانند حرارت را با حداقل اتلاف انرژی از جریانهای خروجی داغ به جریانهای ورودی سرد انتقال دهند ، انجام میشود.
استفاده از مبدل های حرارتی پیشرفته با طراحی بهینه سطح انتقال حرارت و انتخاب مواد مناسب با مقاومت بالا در برابر خوردگی ، به افزایش راندمان بازیافت انرژی و در نتیجه کاهش چشمگیر هزینه های انرژی در تولید اسید نیتریک کمک می کند. این امر نه تنها اقتصادی تر بودن فرایند را تضمین میکند ، بلکه به کاهش ردپای کربنی واحد صنعتی و حفاظت از محیط زیست نیز کمک خواهد کرد.
آینده فرآیند استوالد: نوآوری در کاتالیزور ، فناوری سبز و کاهش آلایندگی
آینده فرآیند استوالد به شدت به نوآوری در کاتالیزورها و بکارگیری فناوری های سبز گره خورده است. کاتالیزورهای پلاتینی کنونی گرچه کارآمدند ، اما گرانقیمت ، کمیاب و به مسمومیت حساس هستند. تحقیقات فعلی بر روی جایگزین های مقرون به صرفهتر و پایدارتر مانند کاتالیزورهای فلزی پایه (مانند آهن، کبالت و نیکل) با ساختارهای نانومقیاس و مواد پشتیبان پیشرفته متمرکز شده است.
هدف ، توسعه کاتالیزورهایی با فعالیت بالاتر، دوام بیشتر و مقاومت در برابر مسمومیت است که منجر به افزایش راندمان فرآیند ، کاهش مصرف انرژی و در نتیجه کاهش ردپای کربن میشود. استفاده از روش های تولید سبز و سازگار با محیط زیست ، به همراه بهینه سازی و کنترل دقیق پارامترهای فرآیند ، نقش کلیدی در آیندهی استوالد ایفا میکند. این امر شامل بهینه سازی مصرف انرژی از طریق بازیافت حرارت و انتخاب منابع انرژی تجدیدپذیر است.
علاوه بر این ، کاربرد فناوری های دیجیتال مانند هوش مصنوعی و یادگیری ماشینی ، برای نظارت بر فرآیند ، بهینه سازی شرایط عملیاتی در زمان واقعی و پیش بینی خطرات و مشکلات احتمالی ، بسیار امیدوارکننده است. این فناوری ها می توانند منجر به تولید اسید نیتریک با راندمان بالاتر ، مصرف انرژی کمتر و آلودگی کمتر شوند. و به پایداری بیشتر و اقتصادی تر بودن این فرآیند کمک کنند.